A unique vertical process: from the purchase of pure elements to the alloy melting, all the way to components manufacturing, entirely custom made.
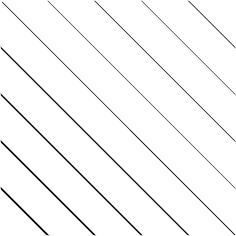
SE
The Superelastic Effect (SE) is the ability of Shape Memory Alloys to fully recover from significant deformation, exceeding the capabilities of conventional materials and alloys. This makes SMA ideal for use in implantable medical devices.
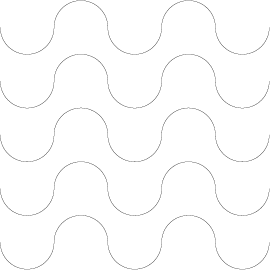
SME
The Shape Memory Effect (SME) allows Shape Memory Alloys to “remember” their original shape and return to it when overheated, enabling unique functionalities in various industries such as automotive, electronics and medical.
A well known material that few can manage.
The origins of Shape Memory Alloys (SMA) trace back to the Naval Ordnance Laboratory, where disruptive innovation experiments led to the discovery of Nitinol. This family of alloys encompasses a wide range of materials, with miniscule changes in chemistry resulting in dramatic changes in properties. The production of functioning SMA requires the most advanced metallurgy processes and the tightest control during conversion.
Only a select few companies worldwide have mastered this intricate niche of science. Ni-based SMA are the most widely used due to their availability, extensive conversion industry, and versatile functional properties. By controlling the chemistry and microcleanliness, performance can be fine-tuned to achieve both Superelasticity and Shape Memory.
A complex manipulation process that starts from nickel and titanium.
Shape Memory Alloys (SMA) are a family of high-tech materials that begin with the basic elements of nickel and titanium. The addition of other elements can dramatically alter the final properties, making it suitable for a wide range of applications. The journey from raw materials to finished product involves a multitude of options, from melting techniques to ingot sizes, and from hot to cold conversion. Every processing step has an impact on the properties and performance of the final component, whether it’s a wire for electrical actuators, a spring for thermostats, or a medical implant. The most critical step is the final thermomechanical processing, also known as training or shape setting, where the properties of the material are set and fine-tuned to meet the specific needs of the application. At the cutting-edge of technology, SMA is a truly remarkable material with limitless possibilities.
Endless possibilities are enabled by the material’s advanced properties.
Shape Memory Alloys (SMA) offer a world of possibilities with their unique combination of size, shape, and geometry versatility. The Shape Memory Effect (SME) is activated by a change in the component’s lattice structure, transforming from martensite to austenite and resulting in a change in shape and mechanical properties. These materials are revolutionizing the automotive, medical, and electronics industries with their lightweight, compact, energy-efficient, and noiseless electrical actuators.
Additionally, the Superelastic Effect (SE) is making waves in the medical field, where it is being used in implantable devices such as stents and aortic valves, thanks to its ability to fully recover significant deformation beyond that of conventional materials. SMA truly is a material of the future, changing the way we live and work.
Temperature and stress causes shift in materials crystalline structure between these two phases which lead to Shape Memory Effect.
3 crystal structures
The three different crystal structures in Shape Memory Alloys are Martensite, Austenite, and twinned Martensite.
- Martensite is a highly distorted, low-temperature crystal structure.
- Austenite is a high-temperature, stable crystal structure.
- Twinned martensite is a partially transformed mixture of Martensite and Austenite.
2 phases
The phase transition from Martensite (Low Temperature Phase) to Austenite (High Temperature phase) in SMAs occurs due to changes in temperature or stress, causing the crystal structure to change from a distorted Martensite form to a more stable Austenite form.
This results in recovery of the original shape.